Tesla Gigafactory offers lessons if EV battery production moves to US
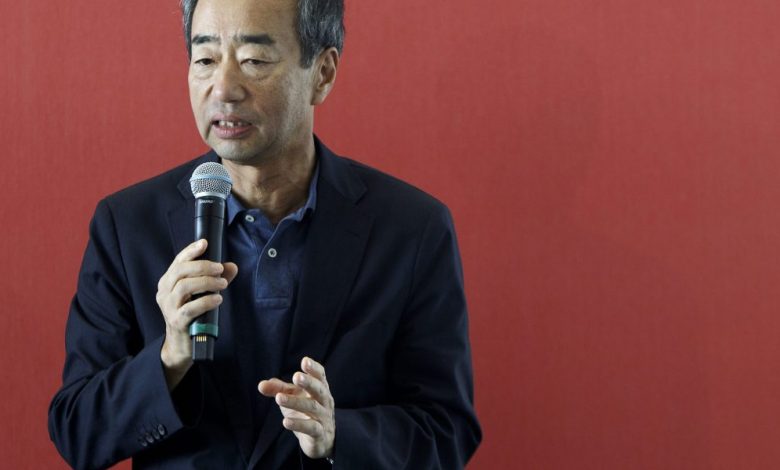
Manufacturing batteries for electric vehicles is tricky work. More Americans will do so in the coming years, thanks to government incentives enticing companies to locate EV battery manufacturing in the US rather than Asia.
At Tesla’s Gigafactory in Nevada, where production began in 2016, battery cell partner Panasonic has employed thousands of workers in its operations within the sprawling facility for years — and has learned some important lessons along the way.
Among them: American workers’ hands are sometimes too big to operate machines from Asia efficiently.
“It sounds like a joke, but such problems were common in the early stages,” said Yasuaki Takamoto, head of Panasonic’s EV battery business Wall Street Journal.
Unexpected difficulties are also likely to arise in similar installations planned by automakers and their battery partners in the US. Last month, Honda and LG announced a joint venture to build such a facility in Ohio. In December, Hyundai and SK announced a similar collaboration in Georgia. Panasonic itself began building another battery factory for electric vehicles in Kansas in November. Vietnamese company Vinfast will manufacture batteries and vehicles for electric vehicles in North Carolina. GM and LG are developing new EV battery factories, one of which is already operational in Ohio. BMW has signed a deal with Envision AESC of Japan to supply battery cells near its South Carolina plant, where the company will invest $1 billion in electric vehicle manufacturing.
For Panasonic, shifting production of lithium-ion batteries from East Asia – where they were traditionally manufactured – to North America presented further challenges diary reported Friday. First of all, even the slightest exposure to moisture can mean batches of product have to be thrown away, so proper training of staff is crucial. And special equipment used in Asia may not pass the test in the US, which has different safety standards and operating conditions.
Such problems, Takamoto said diary, meant ramping up production took a year or two longer than the Japanese company had anticipated. The time required to train workers has also slowed down GM-LG’s battery plant in Ohio, GM CEO Mary Barra said in October.
Another challenge is to design the huge production facilities yourself diary reported. Given the level of outsourcing that has taken place in America over the past few decades, not many builders have recent, relevant experience building the type of massive production facilities that electric vehicle battery manufacturers require.
Learn how to navigate and build trust in your organization with The Trust Factor, a weekly newsletter exploring what leaders need to succeed. Login here.